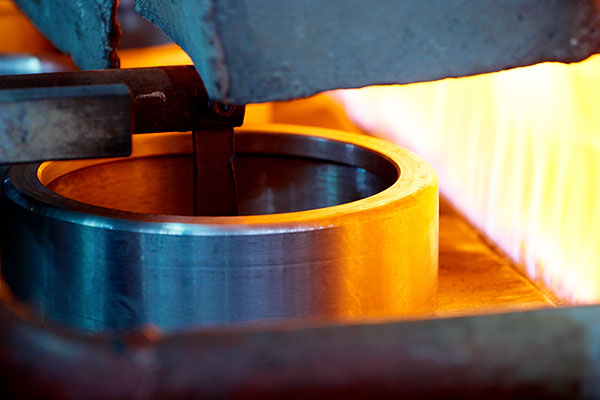
Hot Work Tool Steel
Hot Work Tool Steel are steels capable of withstanding high abrasion, heat and pressure conditions that prevail in manufacturing units that perform processes such as forming, shearing and punching of metals at high temperatures of 480 to 760°C (900 to 1400°F). These steels have wear resistance up to 540°C (1000°F).
Hot work tool steels stand as the vanguard of industrial forging and molding processes, their resilience and thermal stability shaping the very foundation of modern manufacturing. Unlike their cold work counterparts, these steels are tailored to withstand the intense heat and mechanical stress of high-temperature applications, from hot forging and die casting to extrusion and glass processing.
Forged through the crucible of metallurgical ingenuity, hot work tool steel are meticulously crafted to endure the punishing environments of molten metals and high-temperature operations. Their alloy composition, typically enriched with elements like chromium, molybdenum, tungsten, and vanadium, imparts exceptional heat resistance and strength, enabling them to maintain their structural integrity even at temperatures exceeding 600°C (1112°F).
At the heart of their performance lies their ability to resist thermal softening and deformation under prolonged exposure to extreme heat. This property ensures that hot work tool steels retain their hardness and dimensional stability, enabling them to withstand the cyclic heating and cooling cycles inherent in hot forming processes. Whether it’s shaping red-hot steel billets or molding molten aluminum alloys, these steels provide the necessary toughness and wear resistance to endure the harsh conditions of industrial forging and casting operations.
Moreover, the versatility of hot work tool steels extends beyond their resilience to high temperatures. Their excellent thermal conductivity facilitates rapid heat dissipation, minimizing thermal gradients and ensuring uniform heating across the tooling surface. This not only enhances productivity but also reduces the risk of thermal cracking and premature failure, prolonging tool life and reducing downtime.
As industries continue to push the boundaries of temperature and speed in manufacturing, the demand for hot work tool steels remains steadfast. Ongoing advancements in metallurgy, coupled with innovations in processing technologies, drive the evolution of these steels, unlocking new frontiers in productivity and efficiency. From automotive and aerospace to plastics and glass industries, hot work tool steels stand as stalwart guardians of progress, enabling the realization of complex designs and the manufacture of precision components in the crucible of high-temperature production environments. Contact us.