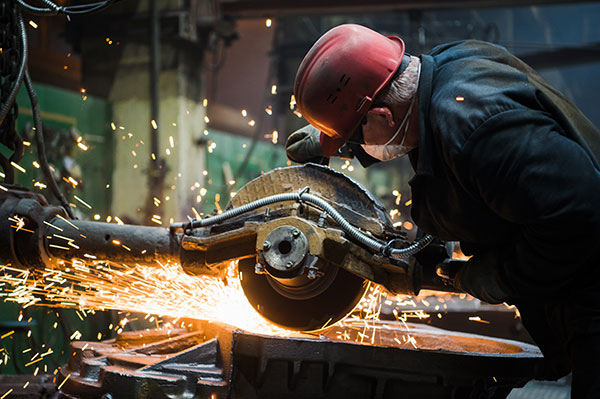
Cold Work Tools Steel
Cold work tool steels are the unsung heroes of manufacturing, silently supporting industries by shaping, cutting, and forming materials with precision and durability. Unlike their counterparts, which excel in high-temperature environments, cold work tool steel thrive in the realm of ambient temperatures, making them indispensable in applications where toughness, wear resistance, and dimensional stability are paramount.
Crafted through meticulous alloying and heat treatment processes, cold work tool steel are engineered to withstand the rigors of repetitive mechanical stress and abrasive wear without faltering. The key to their exceptional performance lies in their microstructure, finely tuned to balance hardness and toughness. Alloying elements such as chromium, molybdenum, vanadium, and tungsten impart hardness, while careful control of carbon content ensures toughness, enabling these steels to maintain their cutting edge under the harshest conditions.
One of the hallmarks of cold work tool steel is their versatility. From stamping and blanking to shearing and forming, these steels find application in a myriad of industries, including automotive, aerospace, and consumer electronics. Whether it’s shaping intricate components or punching through thick sheets of metal, cold work tool steels deliver precision and reliability, driving efficiency and quality in manufacturing processes.
Moreover, the evolution of cold work tool steel continues unabated, with ongoing research and development efforts aimed at pushing the boundaries of performance. Advanced metallurgical techniques, coupled with computational modeling and simulation, enable engineers to fine-tune the properties of these steels to meet the evolving demands of modern industry. The quest for improved wear resistance, toughness, and machinability drives innovation in alloy design and heat treatment methodologies, ensuring that cold work tool steels remain at the forefront of materials technology.
As industries strive for greater productivity and competitiveness, the role of cold work tool steel in shaping the future of manufacturing becomes ever more critical. Their ability to endure the relentless demands of industrial production, coupled with their adaptability to diverse applications, cements their status as indispensable assets in the arsenal of modern engineering. In the hands of skilled craftsmen and technologists, cold work tool steels continue to carve the path towards innovation and progress.
Cold work tool steel are high carbon steel containing smaller amounts of manganese, tungsten, molybdenum, and chromium. They have good dimensional stability and hardenability. They are further classified into three subgroups: Air-hardening steels. High-carbon, high-chromium steels. Contact us.